Back to Listing
How to Minimise Downtime with Efficient Roll On/Off Container
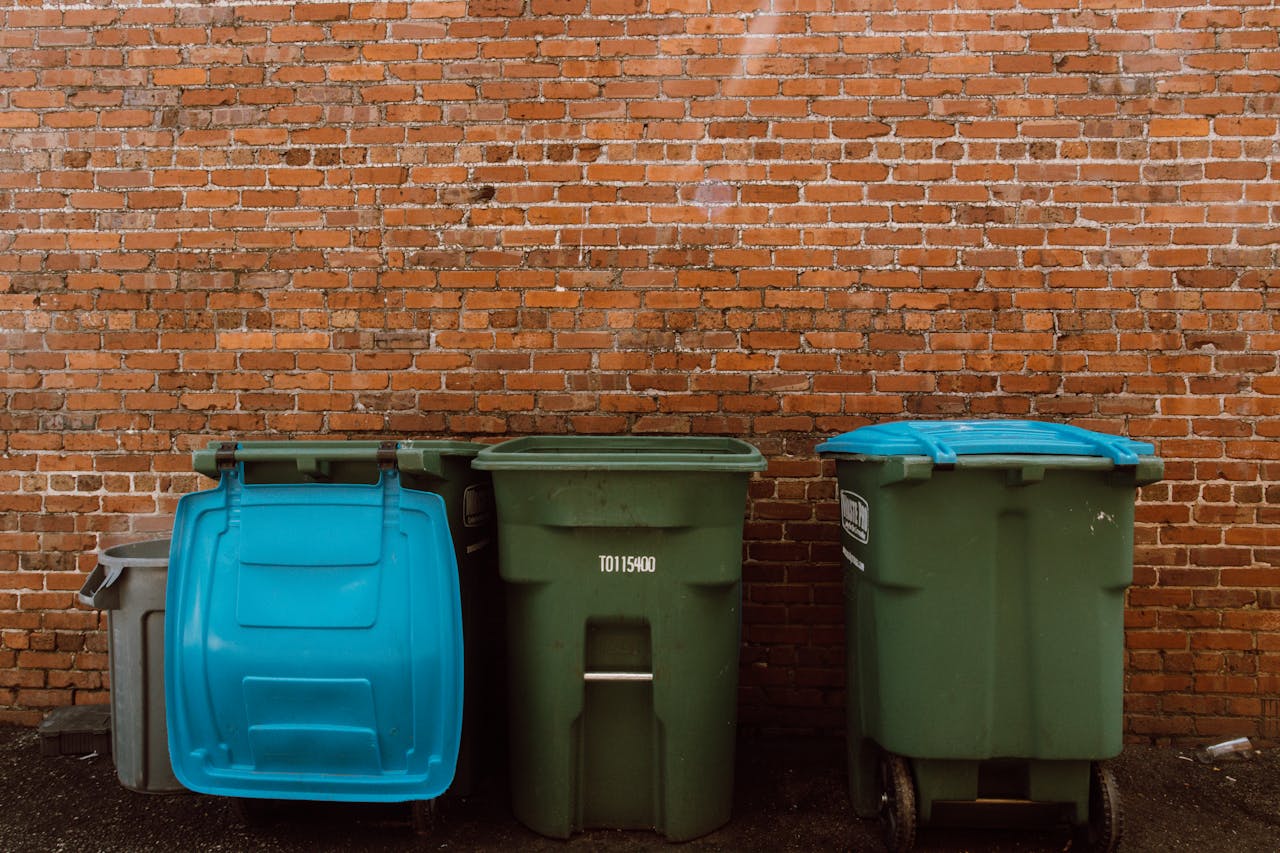
Turnaround: Strategies for Streamlined Operations
Minimising downtime in your roll on/roll off (RoRo) operations is critical for improving efficiency and productivity. You can achieve this through streamlined processes that enhance reliability and speed. By implementing effective strategies, you can significantly reduce turnaround times and increase customer satisfaction.
To get started, focus on utilising technology and best practices that facilitate quick and efficient loading and unloading. This involves the use of automated systems and real-time data to coordinate the movement of containers seamlessly. When everything works in harmony, you not only boost productivity but also improve the overall reliability of your operations.
Investing in proper training for your staff is another essential step. When your team understands the best practices for RoRo operations, they can respond quickly to any issues that arise. This not only decreases downtime but also enhances the service quality you provide to your customers.
Understanding Roll On/Off Container Systems
Roll on/roll off (RoRo) container systems are essential in streamlining the transportation of goods and waste. Their design promotes efficiency, reduces turnaround times, and enhances operational reliability. This section will explore the key components of RoRo systems, their significance in waste management and recycling, and the benefits of ensuring efficient container turnaround.
Components and Functionality
RoRo container systems consist of several key components that work together to facilitate smooth operations. These include:
- Ramps: Built into vessels or transport vehicles, they enable containers to be driven on or off easily.
- Hoisting Systems: Commonly found in ports, these include equipment like cranes and straddle carriers, used for lifting and positioning containers.
- Secure Lashing Systems: These systems ensure containers are stably secured during transport, preventing damage.
Each component contributes to the functionality of the entire system, allowing for quick loading and unloading. This efficiency minimises delays in operations, which is crucial for maintaining deadlines and reducing the overall duration of transport cycles.
Importance in Waste Management and Recycling
RoRo systems play a vital role in waste management and recycling efforts. Their ability to transport large volumes of waste efficiently helps companies reduce their carbon footprint. By facilitating quicker turnover of containers, RoRo systems ensure that waste is processed swiftly, promoting environmental sustainability.
Moreover, these systems enable seamless movement between collection points and recycling facilities. The faster waste can be moved, the quicker materials can be recycled, thus supporting a circular economy. Efficient waste management also leads to reduced operational costs, making it an attractive choice for businesses.
Benefits of Efficient Container Turnaround
Efficient container turnaround has numerous advantages for businesses that rely on RoRo systems. Firstly, it increases operational reliability, allowing you to maintain consistent schedules. A well-optimised turnaround reduces downtime, which can improve overall productivity.
Secondly, reducing the duration of each transport cycle can lead to significant cost savings. Reduced fuel consumption and lower maintenance costs are direct results of improved efficiency. Additionally, these practices contribute to a smaller environmental footprint by optimising logistics and minimising waste generation.
Incorporating efficient RoRo systems not only strengthens your operations but also aligns your business with sustainability goals, benefiting both your bottom line and the planet.
Strategic Planning for Optimised Operations
Effective strategic planning is crucial for minimising downtime in roll on/roll off container operations. This involves assessing current processes, implementing automation, and maximising space use to improve overall efficiency.
Assessment and Process Improvement
Start by regularly assessing your current processes. Identify bottlenecks that slow down container turnaround times. Gather data on loading, unloading, and transport times to pinpoint areas needing improvement.
Use this information to implement process improvement strategies. This may involve revising loading techniques or changing how containers are staged for quicker access. Organise training sessions for your team to ensure everyone understands the new processes.
By continuously monitoring and refining operations, you can increase productivity and reduce downtime.
Automation and Technology Solutions (TAS, TOS)
Integrate automation and technology solutions to streamline operations. Systems like Terminal Operating Systems (TOS) can significantly enhance the management of container flow. These systems provide real-time tracking, reducing the likelihood of human error.
Consider using automated stacking cranes and other machinery to handle containers more efficiently. This reduces the need for manual labour and speeds up the loading and unloading processes.
Investing in technology can lead to noticeable improvements in turnaround times and operational efficiency. Automating repetitive tasks allows your team to focus on more complex issues.
Effective Utilisation of Space
Optimising space is vital for reducing downtime in container operations. Properly layout your container yard to facilitate efficient movement and access. Place frequently used containers closer to operational zones to minimise travel time.
Consider vertical stacking solutions where applicable. This can increase capacity without requiring more land. Additionally, implement clear signage and markings for pathways to enhance navigation within the yard.
Regularly review space utilisation data to adjust your layout as needed. This ensures that your operations remain efficient as container volumes change. Applying these strategies can lead to significant enhancements in your container turnaround efficiency.
Enhancing Safety and Reducing Environmental Impact
Improving safety and minimising environmental effects are crucial when using Roll On/Roll Off (RoRo) containers. Effective safety measures can protect your team, while eco-friendly practices help in protecting the planet. This section addresses important protocols and habits that can lead to a safer and greener operation.
Safety Protocols and Training
Implementing robust safety protocols is vital for protecting workers during the loading and unloading of RoRo containers. You should ensure that all staff members undergo thorough training. This training should include:
- Safe operation of loading equipment
- Proper lifting techniques
- Emergency response procedures
Conduct regular drills and refreshers to keep safety top of mind. Adopting a safety-first culture encourages workers to report hazards and suggest improvements. Regular safety audits and checks help identify potential risks early, ensuring that your team works in a secure environment.
Environment-Friendly Practices
Incorporating environmentally friendly practices can significantly reduce the ecological footprint of your operations. For instance, you can use biodegradable materials for packaging to minimise waste.
Also, consider optimising routes for transport to reduce fuel consumption.
Implementing a recycling programme for waste generated during container operations helps further lessen environmental impact.
Regularly assess these practices to ensure they remain effective and compliant with environmental regulations.
Reducing Carbon Emissions
Reducing carbon emissions is essential for sustainability. You can lower your carbon footprint by upgrading to energy-efficient machinery and vehicles.
Utilising hybrid or electric vehicles for transport is another smart move. Track and monitor fuel usage to identify areas for improvement.
Encourage your team to adopt practices like carpooling or using alternative transport for short distances. This not only reduces carbon emissions but also promotes team bonding.
By being proactive in these areas, you contribute positively to both your operation’s safety and the environment.
Operational Tactics for Maximal Throughput
To achieve high throughput in roll-on/roll-off container operations, focusing on specific tactics is essential. Each tactic improves the flow of containers and minimises delays, enabling you to handle more shipments efficiently.
Gate Process Optimisation
A streamlined gate process is vital. Consider implementing a pre-arrival system that allows drivers to complete paperwork before arriving. This reduces time spent at the gate.
Utilise technology to track and manage container movements. Electronic gate logs and automated check-in systems can help speed up the process.
Construct dedicated lanes for different types of vehicles. This ensures that roll-on and roll-off containers are processed without unnecessary delays. Frequent monitoring allows you to adjust to patterns and predict peak times effectively.
Versatility and Custom Solutions
Flexibility in your operations will cater to varying demands. Custom solutions can be designed to meet specific port needs.
Tailor processes for different container types, such as standard containers and specialised cargo. For example, if you regularly handle oversized loads, create specific procedures for their efficient processing.
Test and implement adaptable staging areas based on current demand. This versatility decreases waiting times and increases the overall efficiency of your operations.
Collaboration with Freight Forwarders
Working closely with freight forwarders can lead to significant improvements in throughput. Establish clear communication channels to share schedules and updates on container availability.
Regular meetings can help align goals and expectations. With coordinated efforts, you can better anticipate needs and avoid bottlenecks.
Use collaboration tools to streamline information sharing. This makes it easier for everyone involved to plan effectively and react quickly to changes, enhancing overall operational efficiency.
Sustaining High Customer Satisfaction and Cost Savings
Maintaining high customer satisfaction while also achieving cost savings is vital for any business. By focusing on quality service and effective resource management, you can create a successful operation that meets customer expectations and keeps expenses down.
Quality Service and Support
Providing quality service starts with understanding your customers' needs. This includes prompt communication and efficient responses to queries or issues. By offering a streamlined service, you not only enhance customer trust but also reduce the time containers spend at the facility.
- Ensure staff are trained to handle different situations effectively.
- Implement feedback systems to identify areas for service improvement.
Additionally, fostering good relationships with customers results in repeat business. When you deliver reliable, high-quality services, customers are more likely to recommend you to others, boosting your reputation in the market.
Cost-Effectiveness and Resource Recovery
Cost savings are crucial for a thriving operation. You can achieve this by optimising container turnaround times and utilising resources effectively. Implementing automated systems and tracking tools can help streamline processes and reduce waste.
- Regularly maintain equipment to prevent costly breakdowns.
- Reassess your supplier contracts to ensure you are getting the best rates.
Resource recovery plays a significant role in keeping costs low. By reusing materials and recycling where possible, you reduce the need for new resources, which also corresponds with your commitment to sustainability. This not only benefits your budget but also appeals to customers who value environmentally conscious practices.
Need professional waste disposal services in London or Essex? Sharp Skips provides dependable options for skip hire, grab loader hire, and roll on off hire, all at competitive rates!